Industrial Melters
WENESCO STANDARD AND CUSTOM MELTERS are constructed of appropriate and tested materials to assure both longevity of the heated tank and uniform heating of your material. Our heating elements are selected and mounted for maximum efficiency and long life. The designs of Wenesco's melters vary according to the melting temperatures and chemical characteristics of the materials to be heated. Wax compounds, hot melt, soap, and other thermoplastics in the 80F to 450F range are best heated using convection heating elements. Soft metal melters require higher watt density elements securely clamped to the tank liner.
Any Wenesco lead melter, zinc melting pot , babbitt melting pot and pewter melting tank can be furnished in a wide selection of shapes and sizes to suit your requirements. All of our melting tanks, including chemical mixing tanks, plastic melters, machineable wax kettles, molten salt tanks and heated blending pots are available in standard models or custom made with special controls. Wenesco gas-fired melting pots are used with natural or propane gas and are fitted with quality temperature and gas flow controls
Such as candle wax, gel wax, soy wax, soap and lubricants are available with pumps and stirrers. 80F -- 250F
For gold, silver, zinc, and most metals with higher melting points. 80F -- 2,300F
For heating and blending a wide selection of compounds including machineable wax, adhesives, plastisol, and hot melt. 80F -- 450
For soft metal & non-metallic compounds. 80F -- 1,050F
For lead, tin, babbit, and other soft metals. Also custom made heated pots with transfer pumps. 80F -- 1,050F
With transfer pumps for most types of eutectic salt. 80F -- 1,110F
Custom Made Melters
Processing Guidelines & Information
HOT MELT PLASTISOLS
When properly compounded, Hot Melt Vinyl Plastisols have sufficient heat stability and flow characteristics to enable the processor to pour or inject the molten compound into a cold or room temperature mold.
At the typical processing temperatures of 330F (166C) to 360F (182C), these compounds exhibit low enough viscosity to allow the plastisol to flow at those elevated temperatures.
When cool, the hot melt plastisol is transformed into a soft rubbery substance.
Vinyl is an excellent thermal insulator. Therefore, it is necessary to continually agitate the compound in the heated vessel. Slow positive agitation, which wipes the surface vessel, will help prevent localized degradation.
It is necessary to keep heat distribution even and below 400F (204C).
The plastisol, as supplied, is a low viscosity liquid. Conversion is accomplished by heating the compound until the polyvinyl chloride resin is solvated by the liquid plasticizers, then further heated to a high enough temperature for proper flow and fusion.
Minimum temperature for fusion is about 330F (166C). Minimum temperatures for molten flow depend upon the compound, its hardness, and the process technique, but could vary from 330F (166C) upward.
Compounds of any color, Including clear, can be utilized. Hardness ranging from 8 Shore A (fish lures) to 30 Shore A (casting molds) can be utilized.
The plasticizers in vinyl are also plasticizers for other plastics and many materials used in paints and lacquers. Prolonged contact, with the vinyl part, can result in plasticizer migration.
PLASTISOL PROCESSING
Melter temperatures should be set to at least 400 F (204 C). Some users
prefer temperature settings as high as 450F (232C), but care must be
exercised as temperatures are increased above 400F (204C).
Uniform heating and reasonably accurate temperature control is important.
A setting of 400F (204C) is used to bring the hot melt to 360F (182C) before pouring.
As the hot melt warms in the vessel, it will begin to phase from a liquid to a solid at around 250F. At this point, it can be visually described as a lump surrounded by liquid. It will remain solid until the temperature reaches approximately 330F (166C) This is normal.
After the plastisol reaches the approximate 330F (166C) temperature, the solid material will begin to phase back into a liquid state.
The hot melt should be stirred during the heating process to assure more uniform heating of the mass. Additionally, the stirring of the mass will help break up the solid phase quicker.
Excessive heat will cause degradation which is evidenced by discoloration, Continued overheating may liberate hydrogen chloride, a corrosive, noxious gas.
OTHER APPLICATIONS
Wenesco stainless Melters are suitable for processing paraffin, animal fats, hydrogenated oils, or any situation where solids and liquids are combined and blended at room temperature, with heat subsequently applied to melt the solids.
Our melters are frequently used for heating and dispensing glue, adhesives, pitch, and tar, Vessels constructed from carbon steel, while cost effective, are porous, and therefore reactive. As a result, with applications where contamination may be an issue, heated stainless steel processing tanks are recommended.
Other applications include waxes for textiles, leather, packagting, metal molding, casting and cosmetics.
Machineable waxes, pharmaceutical waxes and automotive waxes are also successfully processed.
Looking for a Plastisol source? Chemonics Corp www.chemionics.com
Some of the many options available to customize standard melters include:
-
Washdown housing and watertight control panels of 304 stainless steel.
-
Special adjustable stands and supports.
-
Cooling coils for fast cooling of heated compounds.
-
Extra smart programmable temperature controls.
-
Manifolds with nozzles to dispense multiple streams of heated material.
-
Light tower with process timers to view status from across room.
-
316 Stainless construction.
-
Gas-fired melters with auto-pilot light for natural or LP gas, with digital temperature control.

(Left) This custom made 250-gallon melter is made with a long sloping funnel leading to a large, heated drain valve. The melter is controlled with a remote digital controller at 400F. A stirrer maintains the consistency of a special wax compound during the melt cycle. This melter will be mounted later onto a stand, to allow room for a container under the drain..
UNIQUE REQUIREMENTS? Wenesco specializes in custom designs according to your specifications. Ask your sales representative for details.
Customized/Special Melting Pots
We welcome the opportunity to quote on custom melting pots for soft metals up to 1000F.
We have designed and built industrial melters in many shapes and sizes to suit a wide scope of applications.
to head over to our customization request page and fill out the questionnaire to receive more information and a quote.




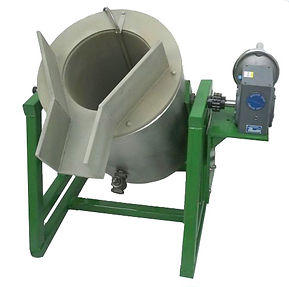
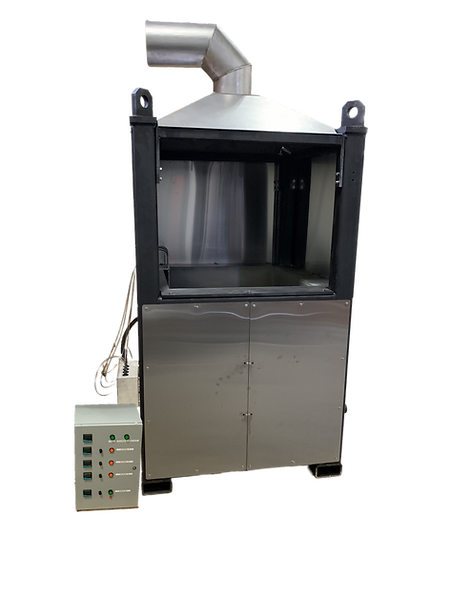
For more info on Melters for strippable plastic coatings, click HERE